A century ago, a team of professors from Harvard University and the Massachusetts Institute of Technology (MIT) embarked on an eight-year study at Western Electric Co.’s massive Hawthorne Works on the West Side of Chicago. Using traditional time-and-motion techniques, they examined how fatigue, monotony and supervision on an assembly line can affect productivity.
Among other things, the landmark human behavior research revealed the Hawthorne Effect. The experiments encouraged the development of human factors engineering and ergonomics, and they put pressure on manufacturers to change the traditional way of managing human resources.
Back in the mid-1920s, those researchers were armed with state-of-the-art tools such as stopwatches and clipboards. Today, manufacturing engineers can improve productivity, quality, ergonomics and safety by harnessing artificial intelligence technology.
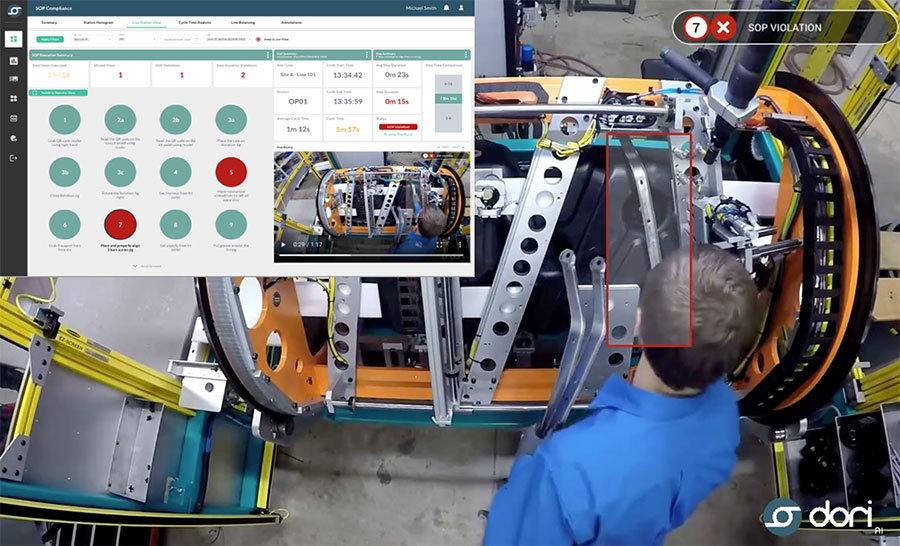
AI technology provides real-time guidance and monitoring for operators. Photo courtesy Dori Inc.
“The biggest advantage of using AI on manual assembly lines is its ability to provide real-time guidance and monitoring, ensuring operators follow standard operating procedures precisely,” says Nitin Gupta, Ph.D., vice president of Dori Inc., which has developed a no-code digital platform called Dori AI. Using computer vision and deep learning video analytics technology, the system monitors plant floor operations.
“AI not only reduces errors, but also enhances consistency, enabling manufacturers to maintain high quality standards while minimizing waste and rework,” explains Gupta. “It improves productivity and efficiency by automating repetitive quality checks, monitoring operator performance and identifying bottlenecks in real-time.”
According to Gupta, AI-powered workstations can detect assembly delays, guide operators to optimize tasks and provide actionable insights to supervisors, leading to streamlined workflows and maximized throughput.
“AI eliminates errors by detecting defects, identifying incorrect components and ensuring adherence to standard operating procedures in real time,” claims Gupta. “By providing instant feedback to operators and capturing anomalies during the assembly process, manufacturers can address issues at the source, leading to higher yields, reduced scrap rates and improved customer satisfaction.”
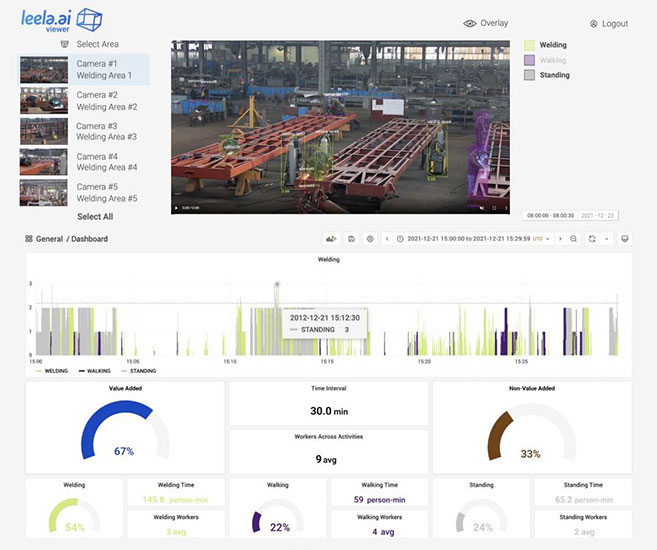
This dashboard generates real-time graphics for tracking and visualizing manufacturing operations. Illustration courtesy Leela AI
“AI technology revolutionizes manual assembly lines by bridging the gap between human expertise and machine precision,” notes Elsa Man, director of marketing at Retrocausal Inc., which has created tools such as Assembly Copilot and Kaizen Copilot. The generative AI-powered, video-based continuous improvement software is used by a variety of manufacturers, including Bosch, Boston Scientific, Carrier, Denso, Honda, Siemens, Stellantis, Stryker and Yamaha.
“The key advantage is its ability to provide real-time support to operators and engineers alike,” says Man. “For operators, AI offers step-by-step guidance through complex assembly tasks, ensuring consistency and accuracy without requiring advanced technical training.”
Benefits to Operators and Engineers
Assembly Copilot leverages machine learning and computer vision to guide operators and instantly flag errors. That helps reduce cognitive strain and builds confidence in task execution.
“For engineers, AI eliminates the time-consuming aspects of manual data collection and analysis,” notes Man. “Traditional methods require repetitive observations, note-taking and calculations to identify inefficiencies. With AI, engineers can gain actionable insights and recommendations from a single cycle video, drastically reducing the time spent on diagnostics and enabling them to focus on implementing improvements.
“This dual empowerment of operators and engineers creates a more agile, efficient and error-resistant assembly process,” claims Man.
“Today, manufacturers in a variety of industries want to optimize manual assembly tasks,” adds Cyrus Shaoul, Ph.D., CEO of Leela AI, an MIT spinoff that has developed visual intelligence software that identifies and times every step in the manufacturing process to spotlight bottlenecks and best practices.
“Leela Platform helps improve productivity by comparing performance across shifts and locations,” explains Shaoul. “It can spot safety violations and optimize staff redeployment.”
Leela Platform acts like an always-on time-and-motion study, identifying and tracking frontline activities as people interact with tools, machines, parts and products. The software provides insights that enable [engineers] to identify bottlenecks and best practices, and compare productivity between shifts, workstations and locations.
“The only way to get that data reliably and at scale is with sensors and an AI system that can understand what the sensors are picking up,” says Shaoul. “Our system is like running a very powerful time-and-motion study on every cycle and every stock keeping unit (SKU) that is assembled.
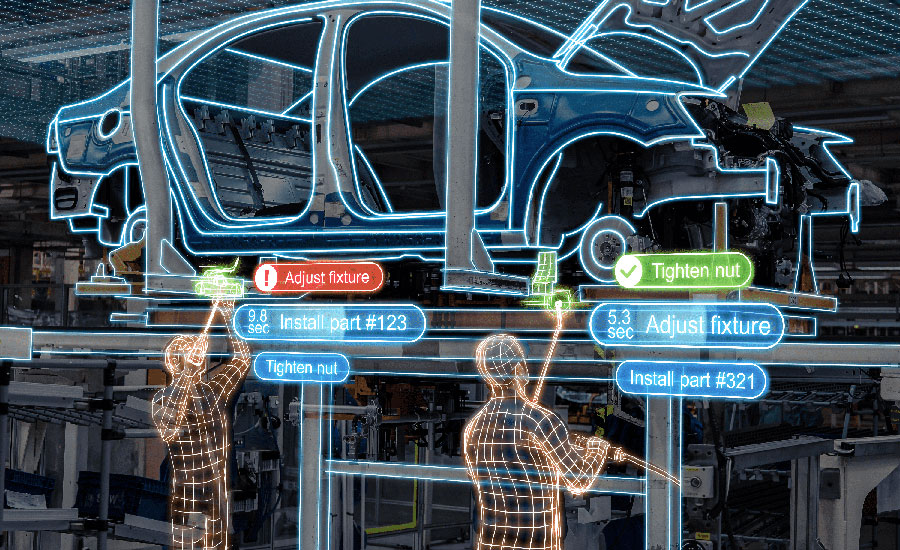
AI technology revolutionizes manual assembly lines by bridging the gap between human expertise and machine precision. Illustration courtesy Retrocausal Inc.
“In the old days, engineers had to conduct time-motion studies by hand, using a stopwatch,” notes Shaoul. “That was a very slow, time-consuming process. It required someone to walk around on a plant floor while watching and measuring assembly tasks.
“That makes it hard to be discreet,” warns Shaoul. “And, being observed always changes human behavior, so the results are often biased and not truly reflective of normal production activity.
“Our system analyzes video in real time, providing a stream of data,” says Shaoul. “The AI technology enables engineers to conduct hundreds of time-motion studies every week. That’s something that wasn’t possible in the past.”
Artificial intelligence technology can help address inefficiencies at every stage of the assembly process. It enables real-time monitoring and analysis, allowing manufacturers to detect and resolve bottlenecks before they escalate into major production delays.
Products such as Retrocausal’s Kaizen Copilot can analyze a video of a workstation to uncover inefficiencies, such as excessive operator movements, unbalanced task allocations or ergonomic risks.
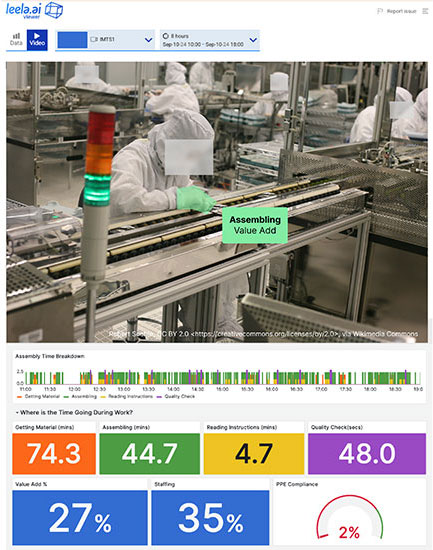
Visual intelligence software measures and analyzes the complex interactions between people, tools, machinery, robots, parts and products. Photo courtesy Leela AI
“These insights lead to actionable recommendations, like reorganizing tools to reduce motion waste or reconfiguring workflows for better line balancing,” explains Man. “By automating these time-intensive analyses, engineers can spend less time on tedious tasks and refocus their resources to optimize processes much faster than traditional methods allow.”
In addition to boosting productivity, applying AI can help manufacturers eliminate errors and boost quality yields.
“Errors in manual assembly processes can be costly, leading to rework, scrap or even product recalls,” laments Man. “AI tackles this problem in two significant ways: prevention and traceability. Through technologies like real-time error detection, AI acts as a safeguard during assembly tasks.”
Assembly Copilot, for example, provides step-by-step guidance and verifies each action in real time. If a worker omits a step or executes it incorrectly, the system immediately alerts them, enabling correction before the error spreads downstream.
“Moreover, AI enhances traceability by maintaining a comprehensive video record of every assembly process,” says Man. “This video traceability helps [engineers] identify the root causes of defects, whether they stem from operator errors, equipment malfunctions or process inconsistencies. By addressing these root causes systematically, manufacturers can boost first-pass yields, reduce waste and maintain higher levels of customer satisfaction.”
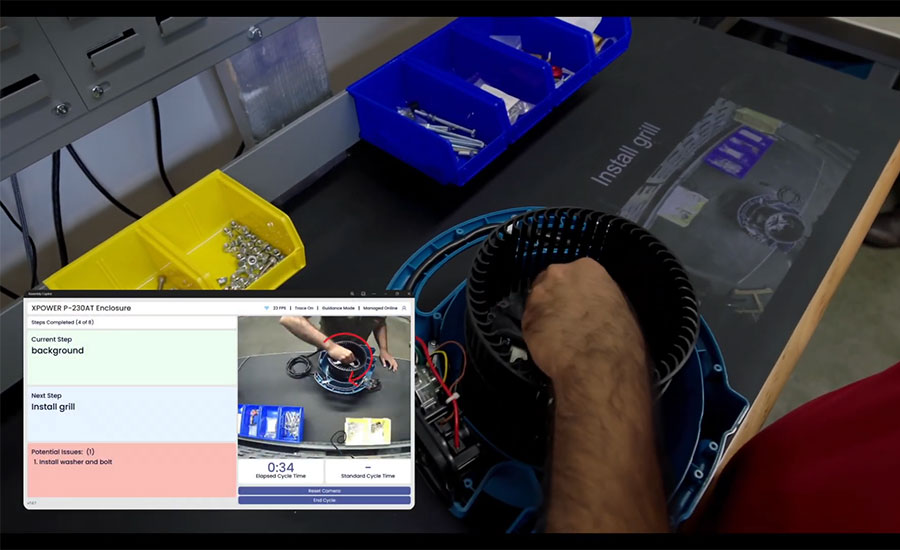
This system can analyze a video of a workstation to uncover inefficiencies, such as excessive operator movements, unbalanced task allocations or ergonomic risks. Illustration courtesy Retrocausal Inc.
Myths and Misperceptions
Artificial intelligence offers numerous benefits to manufacturers, but like any new technology, it’s subject to a variety of myths, misperceptions and misunderstandings.
“The biggest myth is that AI requires complete automation or advanced technical knowledge to implement,” says Dori’s Gupta. “In reality, [the technology] integrates seamlessly into manual workflows, complementing human operators rather than replacing them. These systems are user friendly and scalable, making AI accessible even to small- and medium-sized manufacturers.
“However, a common mistake is expecting a one-size-fits-all solution,” notes Gupta. “Many engineers overlook the importance of tailoring AI models to their specific assembly tasks and operational challenges. In addition, neglecting proper data collection and training can lead to suboptimal performance.”
“One of the most pervasive myths is the fear that AI will displace human jobs,” adds Retrocausal’s Man. “In reality, AI is not a replacement for human operators, but a collaborator. It enhances human capabilities by taking over repetitive, error-prone tasks and providing real-time feedback that enables operators to perform at their best. Far from making humans obsolete, AI is designed to empower workers with tools that make their jobs easier and more efficient.
“Another misunderstanding is that AI is complex, expensive and only suitable for large-scale operations,” Man points out. “This isn’t true. [AI systems] are increasingly accessible, scalable and tailored to the specific needs of manufacturers, regardless of their size. For instance, our Kaizen Copilot tool only requires a smartphone to take a short video to get started.”
Before implementing AI, manufacturing engineers should have a clear understanding of the problem it’s intended to solve. Some companies invest in the technology with the hope that it will be a catch-all solution, only to find it underperforming due to misalignment with their specific challenges.
“Successful AI applications require a targeted approach,” warns Man. “ Engineers should identify the most critical pain points—whether it’s error reduction, cycle time improvement or ergonomic analysis—and apply AI to address those specific issues.
“Another mistake is underestimating the importance of operator buy-in,” says Man. “The success of using AI on manual assembly lines depends on operators feeling comfortable and confident using the technology. Overly complex or intrusive implementations can lead to resistance.”
According to Man, the most successful AI applications are intuitive, minimally disruptive and focused on empowering operators. They offer clear benefits and respect operator privacy.
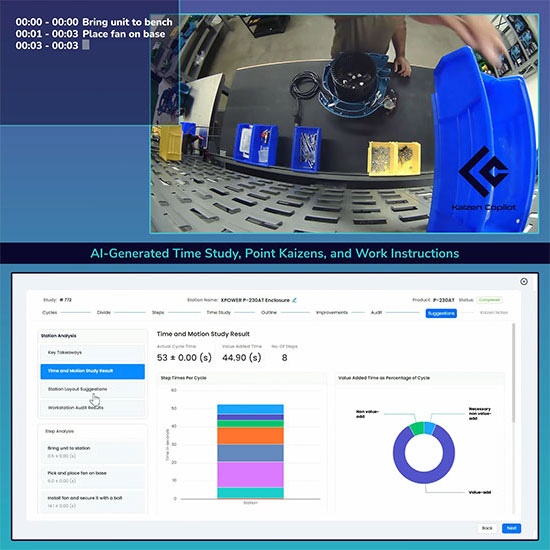
With AI, manual assembly processes that once took weeks to analyze can now be optimized in just hours. Illustration courtesy Retrocausal Inc.
Powerful AI Tools
Engineers have a variety of products available for improving manual assembly productivity, including software and platforms that feature the latest artificial intelligence technology.
Dori AI, for instance, can detect any person, process or asset. Engineers can choose from one of several preconfigured application templates designed to provide intuitive dashboards, interfaces and instant video replay of any event. The software can be configured and deployed on the edge or cloud.
Engineers can easily connect any camera or visual data source, and then deploy and manage thousands of endpoints through centralized dashboards and APIs.
The software turns visual data into predictive AI models. Engineers can monitor workforce movements and activities to improve productivity; ensure standards are followed; detect and flag risks and hazards before they escalate; and monitor how much time workers spend at various tasks or workstations.
Dori’s newest product offering is Kitting Validation, which ensures the right components are included in each kit before assembly.
“What makes it unique is its ability to detect and flag missing, incorrect or misplaced parts in real-time, reducing assembly errors and ensuring smoother downstream processes,” explains Gupta. “By integrating AI-powered visual inspection with real-time alerts, Kitting Validation stands out as a reliable and efficient solution for assembly accuracy.”
Leela AI recently joined Nvidia Metropolis, a partner program, application framework and set of developer tools focused on bringing to market a new generation of vision AI applications. “It nurtures a rich ecosystem and offers powerful developer tools to supercharge vision AI applications that are designed to make the world’s most important spaces and operations safer and more efficient,” says Shaoul.
“Our newest product, Tactsync, was just released last month,” explains Shaoul. “It is designed to help high-mix, low-volume manufacturers. The last time they made a particular product may have been several years ago, and they may not have a good handle on how long something takes to build.
“Tactsync is designed to analyze the cost of labor for each product and create realistic work schedules, which are often lacking in high-mix, low-volume production environments,” says Shaoul. “It helps manufacturers with thousands of SKUs or many different variants build and maintain a reliable data set of median assembly times. Having a standard work measurement for every SKU will help engineers get a better grasp of time expectations and do much better planning.
“Later this year, we’ll be unveiling some additional products and features related to ERP and MES integration,” Shaoul points out.
Retrocausal’s latest product is Kaizen Copilot. The software automatically analyzes video from a workstation, identifies areas for improvement and provides actionable recommendations. Step discovery technology autonomously parses the video into meaningful steps.
Next, it conducts a time and motion study, a failure modes and effects analysis, and an analysis for steps that add value and those that do not. AI then provides recommendations for the most efficient and safe station design, based on Lean Six Sigma and the Toyota Production System. Five integrated modules provide a full suite of capabilities, including line balancing, time and motion studies, FMEA generation, ergonomic analysis and process optimization.
“Kaizen Copilot, redefines continuous improvement for manufacturing by combining simplicity, speed and comprehensive functionality,” claims Man. “Unlike traditional methods that rely on tedious manual data collection or multiple software tools, it extracts actionable insights from a single video of an assembly cycle.
“What makes Kaizen Copilot truly unique is its ability to streamline analysis,” says Man. “By uploading a standard smartphone video, the platform automatically detects, segments and labels each step of the cycle, providing engineers with immediate insights. Beyond saving time, the AI generates actionable recommendations, enabling engineers to focus on implementing meaningful changes instead of spending hours crunching data.
“With Kaizen Copilot, processes that once took weeks to analyze can now be optimized in just hours,” notes Man. “By consolidating multiple tools into a single AI-powered solution, it empowers manufacturers to achieve measurable productivity gains while fostering a safer and more efficient shop floor.”
For more information on AI in manufacturing, read these articles:
Man vs. Machine
The Growing Role of AI in Automotive Assembly
University of Virginia Tackles AI in Manufacturing